Ever wondered how VR and AR devices give you such clear and immersive visuals? It’s all thanks to the latest in THY Precision injection molding optical lenses. Let’s explore the detailed injection molding optical lensesprocess behind these precise components. See how it’s changing the game for the next generation of displays.
Key Takeaways
- Injection molding optical lenses is transforming the production of optical lenses for next-generation display technologies.
- Advancements in injection molding optical lenses techniques enable the manufacture of high-precision optics.
- Strategies to mitigate residual stresses in injection-molded optical components are crucial.
- Innovations in injection molding optical lenses are driving progress in VR, AR, and other display applications.
- Understanding the injection molding optical lenses process step by step is essential for the future of display technologies.
Advancements in Injection Molding for Optical Lenses
At THY Precision, we see the injection molding optical lenses process as key to the future of optical lens technology. With the rise of virtual reality (VR) and augmented reality (AR), the need for precise, injection molded lenses is higher than ever.
Injection Molding optical lensesTechniques for High-Precision Optics
One big leap in making optical lenses is using cyclic olefin copolymers (COC) in the co-molding process. This material makes lens design more flexible and cuts down on surface roughness. This leads to lenses that are clear and precise.
Thanks to COC, making high-precision optics has become easier. This has been key for creating better virtual and augmented reality experiences. It’s changed how we make lenses for these new display technologies.
Reducing Residual Stresses in Injection Molded Optics
Getting rid of residual stresses in optical lenses is also crucial. These stresses can affect how well the lenses work and how long they last. They can cause distortion and make the lenses less durable.
THY Precision has found new ways to tackle this issue. They use advanced tools to fine-tune the injection molding optical lenses process. By controlling things like mold temperature and cooling rates, they’ve cut down on residual stresses. This means they can make high-quality lenses for the latest displays.
Injection Molding optical lenses Technique | Benefits for Optical Lenses |
---|---|
Co-molding with Cyclic Olefin Copolymers (COC) | Improved design flexibility, reduced surface roughness |
Residual Stress Reduction Strategies | Enhanced optical quality, improved durability |
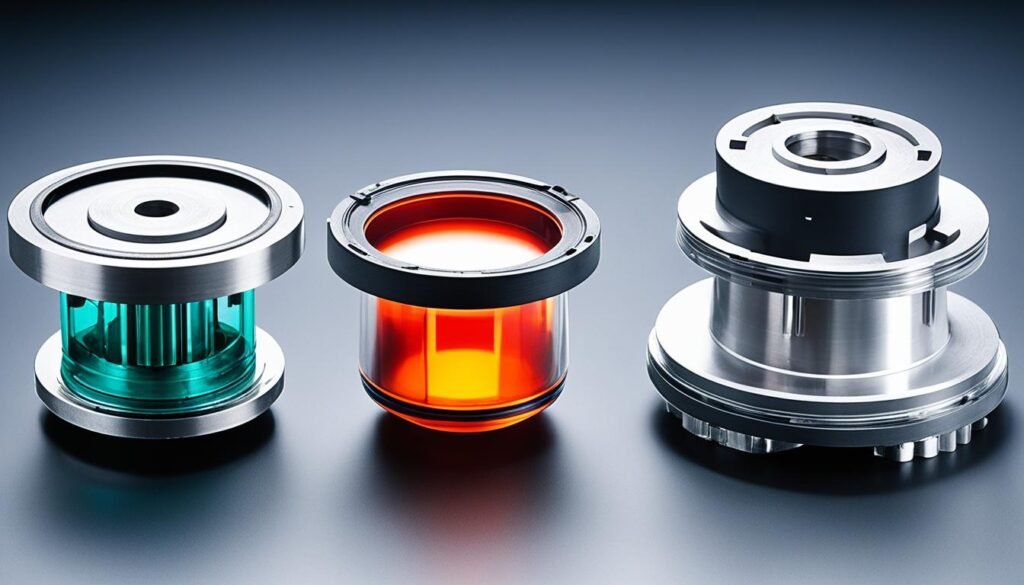
As the need for top-notch, injection molded lenses grows, THY Precision leads the way. They’re always finding new ways to improve the injection molding process. This ensures they can deliver the best optical components for future display technologies.
injectionmoulding processsstepbystep
At THY Precision, we know the details of the injection molding process step by step. This method is key for making high-quality optical lenses for new display technologies. We’ll look at the main stages of the plastic injection molding stages. We’ll see why each step is important for the best performance and precision.
The injection molding cycle starts with getting the mold ready. This means designing and making the mold cavity to fit the lens shape and size. Getting this right is crucial because small mistakes can affect how the lens works.
- Material Selection: Picking the right injection molding parameters is key. THY Precision picks materials that have the right refractive index, transparency, and strength for advanced displays.
- Injection Molding Machine Operation: The machine that injects the plastic is very important in the injection molding process step by step. Our team controls temperature, pressure, and speed to make sure every part is perfect.
- Mold Filling and Cooling: When the plastic goes into the mold, it must fill evenly and completely. Cooling it right is also key to avoid stresses and keep the lens working well.
By getting each injection molding cycle step right, THY Precision makes lenses that meet today’s high standards. Our focus on doing better in the injection molding process step by step makes us leaders in making top-notch optical parts.
Injection Molding Parameter | Importance for Optical Lenses |
---|---|
Melt Temperature | Ensures optimal material flow and viscosity for precise lens shaping |
Injection Pressure | Determines the level of detail and accuracy in the final lens geometry |
Holding Time | Crucial for minimizing residual stresses and maintaining optical clarity |
Mold Temperature | Affects the cooling rate and helps control birefringence and other optical distortions |
At THY Precision, we’re proud of our skill in the injection molding process step by step. We use our knowledge to make top optical lenses for the next generation of displays.
Next-Generation Display Technologies and Optical Lenses
The injection moulding process is changing the game for next-generation display technologies. This is especially true for virtual reality (VR) and augmented reality (AR). Thanks to new advancements in injection molding for optical lenses, we’re seeing top-notch VR and AR optics. These deliver amazing visual experiences to users.
Advancements in Virtual Reality (VR) and Augmented Reality (AR) Optics
The step-by-step injection moulding process has led to the creation of high-performance VR Pancake modules. These modules have better optical performance and are more compact. They aim to give users a real-life, immersive visual experience in virtual reality.
Also, the injection moulding process has made it possible to develop full-color AR surface relief grating (SRG) diffractive waveguide modules. These AR optics are changing how we use augmented reality. They provide clear, high-contrast images that blend well with the real world.
Feature | VR Optics | AR Optics |
---|---|---|
Optical Performance | High-performance Pancake modules | Enhanced full-color SRG diffractive waveguides |
Form Factor | Compact and lightweight | Seamless integration with real-world environment |
User Experience | Immersive and true-to-life | Vivid, high-contrast imagery |
These advancements in VR and AR optics, thanks to the injection moulding process, are changing how we use next-generation display technologies. They offer a peek into the future of virtual and augmented reality.
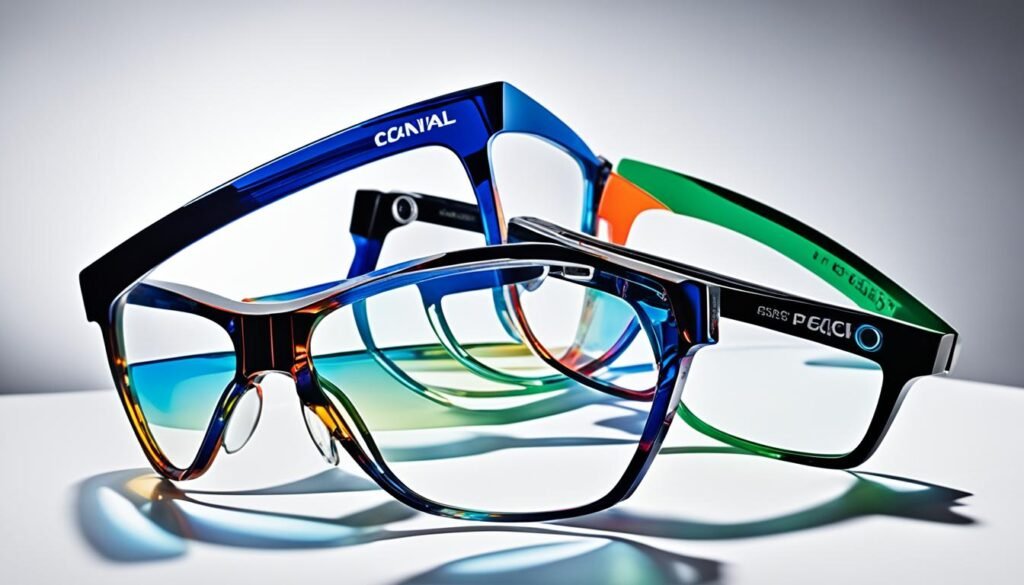
Conclusion
THY Precision’s article on the injection molding process shows its key role in making high-precision optical lenses. These lenses are vital for next-generation display technologies. Thanks to new injection molding techniques, we can now make optical parts for VR, AR, and other displays.
This process has changed the game for display technologies. It makes it possible to create precise and affordable optical lenses. THY Precision uses the latest in injection molding to make lenses that improve experiences in entertainment, healthcare, and more.
As we want more immersive and beautiful displays, injection molding’s role in making optical lenses will grow. THY Precision leads in creating the optical parts for the future of displays. This will change how we interact with and see the digital world.